D
Deleted member 20348
Guest
Edit
There are professional ways to care for bolts, this is not one of them.
The bolts on the rear beam mount were removed one by one.
The simple cleaning process, a Stanley knife blade to scrape off flakes of rust then wire brush and finally grease.





Below is an excellent post by @Indi discussing bolt coatings.
Another couple of great posts by @Little Dog
www.a2oc.net
There are professional ways to care for bolts, this is not one of them.
The bolts on the rear beam mount were removed one by one.
The simple cleaning process, a Stanley knife blade to scrape off flakes of rust then wire brush and finally grease.





Below is an excellent post by @Indi discussing bolt coatings.
Another couple of great posts by @Little Dog
Finding and preparing a new to me AMF
Audi Erwin. https://erwin.audi.com/erwin/logout.do Buy an hour, under a tenner. You get the correct info by VIN. Mac. yeah that's the one I've used for T5 before
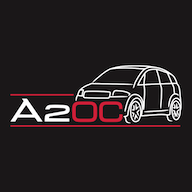
Last edited by a moderator: